January 22, 2024
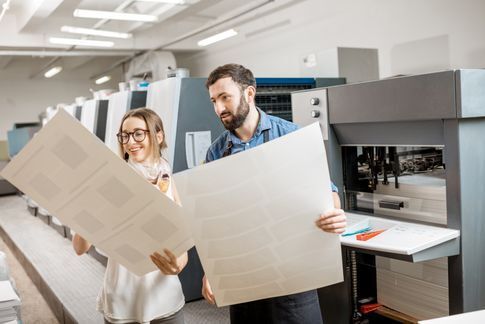
Printing methods are never stagnant. Industries are always looking for new ways to print eye-catching visuals and meet the evolving needs of their clients. From traditional methods to 3D printing, there’s been a printing method that many businesses rely on to accomplish their printing needs excellently: Offset printing.
You’ve likely encountered a product of offset printing before, such as plastic cards or posters. Experts suggest that offset printing will play a substantial role in the growing market, reaching a 1.3% CAGR growth or $862 billion by 2024 when combined with digital printing.
Understanding what offset printing is helps you remain current with changing industry trends and provides relevant services to your customers.
What is Offset Printing?
Offset printing is a technique that uses rollers and rotating cylinders wrapped in a metal plate or blanket to press the ink onto the medium, typically sheets of durable paper. The method doesn’t print ink directly onto the sheet, hence the term “offset printing.”
How offset printing differs from other types of printing
A key element of how offset printing works and what makes it so unique is how the ink arrives on the surface of the medium. Other printing methods apply the ink directly onto the sheet; the process of offset printing, on the other hand, relies on intermediary steps, specifically involving a rolling cylinder and metal-plated blanket.
It’s remarkably similar to flexographic printing, except for a few differences.
One is that flexographic printing typically uses flexible rubber relief plates, while offset printing relies on metal plates for ink transfer. Flexographic printing also applies ink onto raised areas of the plate, while offset printing intentionally uses another roller to separate inks and designs.
Although additional steps may sound inefficient, they make offset printing highly effective for its many purposes. What is offset printing used for? Brochures, magazines, and packaging are just some of its popular use cases. In fact, the diversity of its uses explains why there is more than one type of offset printing.
Types of offset printing
Offset printing processes adapt to client needs, with notable types including:
1. Sheet-fed Offset Printing
Sheet-fed offset printing involves pre-cut pages sent into the offset printer. Some uses for this printing include large run direct mail, catalogs, business cards and high-quality posters.
2. Web Offset Printing
In contrast to sheet-fed, web offset printing involves a continuous sheet of paper that is cut later on. It’s an efficient method for editorial work, including books and newspapers.
3. UV Offset Printing
UV offset printing uses ultraviolet light to dry the ink quickly, which makes the process even more efficient. The packaging industry benefits from UV offset printing the most since it retains the vibrancy and fidelity of the print on different surfaces.
How Offset Printing Works
Offset printing uses various cylinders and plates to create a smooth printing process. Here’s a behind-the-scenes look at how it all works.
Calibrating printers and designs
Clients will have to work closely with the graphic designers and pre-press operators to prepare the image digitally for printing. This primarily involves optimizing the colors of the print to highlight the cyan, magenta, yellow, and black (CMYK) color groups. Adjustments might include enhancing black with cyan, magenta, and yellow, to create a “rich black” hue, for instance.
The ink then goes through various rollers and cylinders, starting with the plate cylinder.
Preparing plates
Offset printing plates are often either metal, paper, or plastic. Operators will place the client’s designs onto these plates. These receive the ink and wrap around the plate cylinder, which also touches the blanket cylinder.
While the plate cylinder revolves, dampening rollers apply water to non-image sections of the print, and ink rollers apply ink to the image areas. Water is essential in this process, as its chemical properties repel ink, ensuring distinct separations between colored and non-colored regions on the print.
In effect, the paper traverses through additional cylinders with different colored inks, eventually forming the final product.
Feeding the sheets
After design optimization and plate preparation, sheets ready to receive ink are stacked in the feeding section. Precise air jets push each sheet into the rotating cylinders. This occurs while the blanket-covered cylinder receives the print’s design from the inked plate cylinder.
Interacting with water and ink
The ink from an inking unit travels through rotating rollers before it finally lands on the fed sheet of paper. What’s crucial at this phase of the offset printing process is the chemistry between water and ink. Their non-mixable properties create a precise print. Offset printers will place water onto areas of the plate without designs to allow the ink to travel to the colored sections.
Drying the sheet
The printer deposits the printed sheet onto a stack on the other end. Since the ink will still be fresh at this point, machines will spray anti-set-off powder to prevent the stack from sticking to itself. Depending on the type of printing, operators will then use guillotine to shape and trim the sheets according to the brief.
5 Advantages of Offset Printing
There are several reasons why industries and businesses choose offset printing over other types of printing. Here are some of its advantages.
1. Consistent, high-quality printing
Once operators have calibrated the offset printer, the process becomes considerably smooth. The rollers' ability to consistently produce high-fidelity images ensures that every print looks and feels as fresh as the first. This reliability makes offset printing ideal for projects demanding precision, such as brochures and high-end packaging.
2. Cost-effective for long print runs
The cost of long print runs is what differentiates offset vs digital printing. Once printer operators have set up the offset printer, the cost per unit decreases remarkably with each additional print. In contrast to digital printing, it will often require the printer to recalibrate per order, working slower and costing more.
3. Versatility
Offset printing offers plenty of customization options. You can experiment with different mediums, including paper, cardboard, and metal. This means you have an even greater opportunity to differentiate your brand on the market.
4. Short turnaround time
There’s no question that customers expect to receive their purchases much sooner than before. The set of rollers and cylinders offset printers use allows them to reproduce large quantities of prints efficiently and quickly. These features make offset printing an excellent choice for projects with tight deadlines.
5. Sustainability
In a time when protecting the environment is a top priority, offset printing shines as a highly viable sustainable printing method to keep carbon emissions and waste down while increasing production and quality.
Offset printers often use aluminum printing plates that are long-lasting and highly recyclable. Additionally, printers can use recycled or less toxic ink to cultivate an even more environmentally friendly operation.
Find the Balance of Excellent Printing and Low Costs
It’s always important to keep looking for ways to boost your printing productivity to remain competitive in the evolving market. Offset printing is a cost-effective solution for producing high amounts of print orders that maintain a premium quality.
For extensive design printing needs, consider reaching out to Intermedia Print Solutions. We offer an array of printing services, including offset printing, that you can use to meet customer demands and empower your business strategies.
Reach out and get a quote from us today!